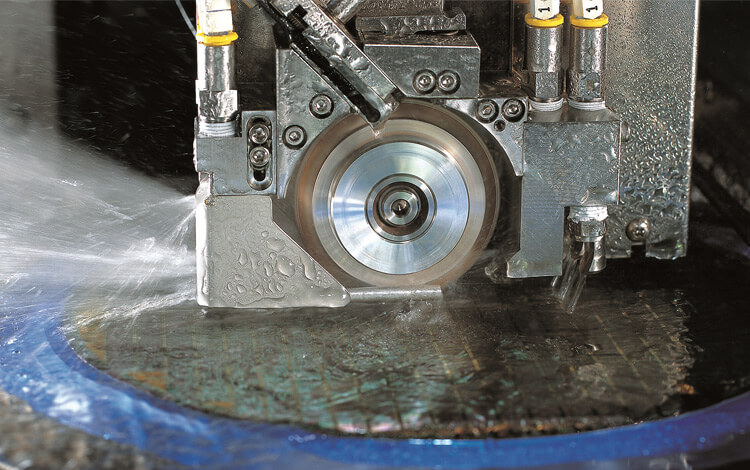
Single Cut
Single cut dicing utilizes a blade to cut all the way through the substrate in one pass. This can be done with a single spindle dicing saw or dual spindles can be used to increase throughput.

Step Cut
Step cut dicing uses dual spindle dicing saws with two different blades. Typically one blade cuts partially into the wafer and a second blade dices the remaining material in the same street. This can help to improve quality including backside chipping as well as dice multiple materials bonded together.
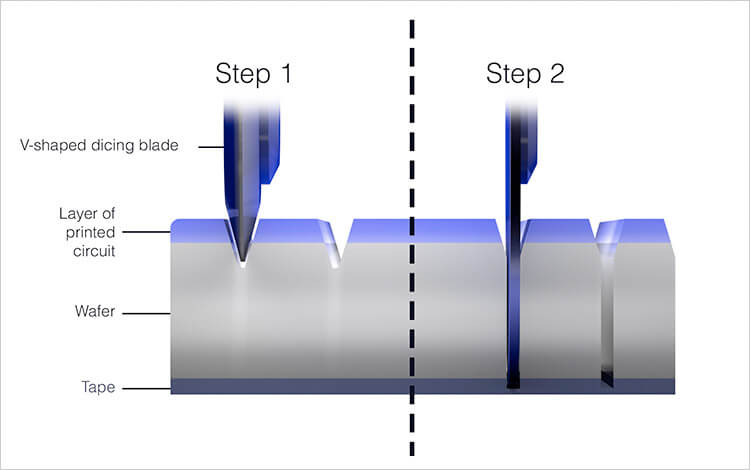
Bevel Cut
A bevel cut process uses one blade with a V-shaped tip to create an angled groove followed by a second blade that cuts through the bulk of the material. This process can significantly improve topside quality and creates an angled topside of the die, which improves die strength.
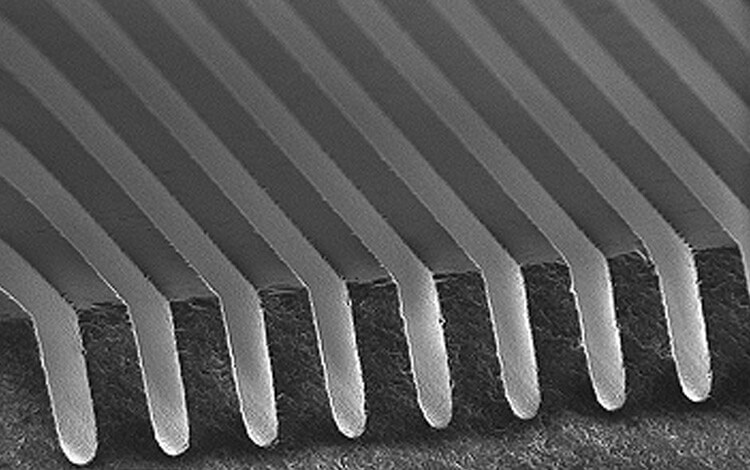
Blade Grooving
DISCO is able to create well formed grooves in materials including piezoelectric ceramics (PZT) for transducer applications.
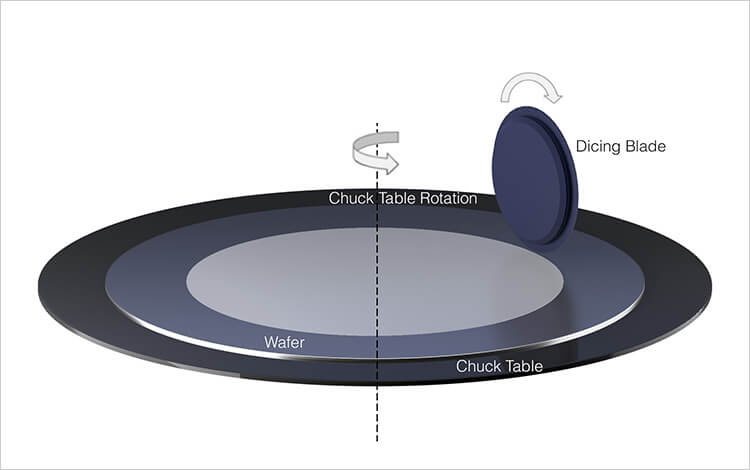
Circle Cut (Wafer Coring)
For wafer downsizing
Circle cut is used to reduce the diameter of a wafer for applications where a smaller diameter wafer is needed. This method utilizes the theta rotation of the chuck table to cut the wafer down to a smaller size in a concentric circle. Flats can be added using this technique as but notches cannot.
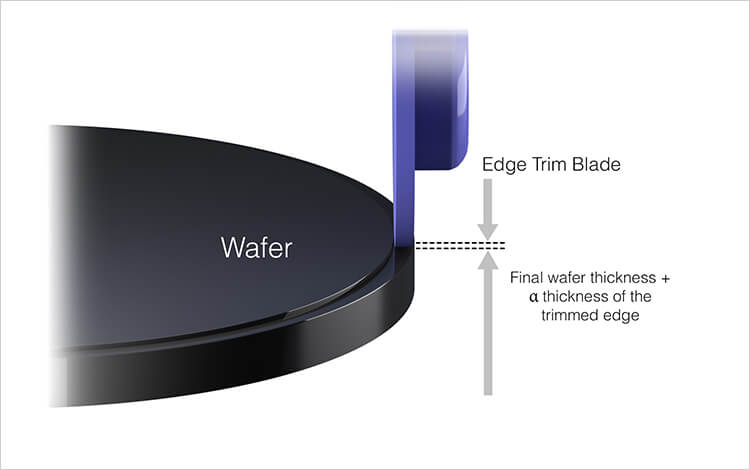
Edge Trim
Edge trim by dicing saw is used when wafers are thinned below 100um. The blade creates a shelf on the wafer surface so that when the wafer is thinned, the wafer edge bevel does not become a knife edge, leading to edge chipping and wafer breakage. It can be used for wafers that will be ground on tape or carrier wafers, as well as bonded wafer stacks.
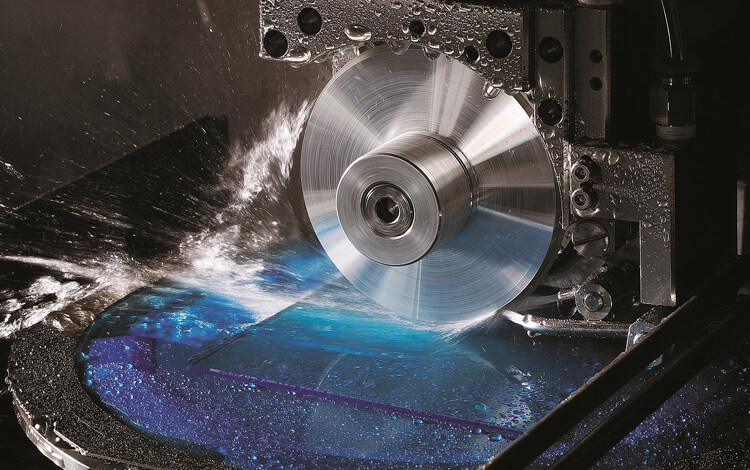
Ultrasonic Dicing
Ultrasonic dicing is used primarily for hard materials such as silicon carbide and can improve dicing quality as well as increase the dicing speed.
Send us your service request now